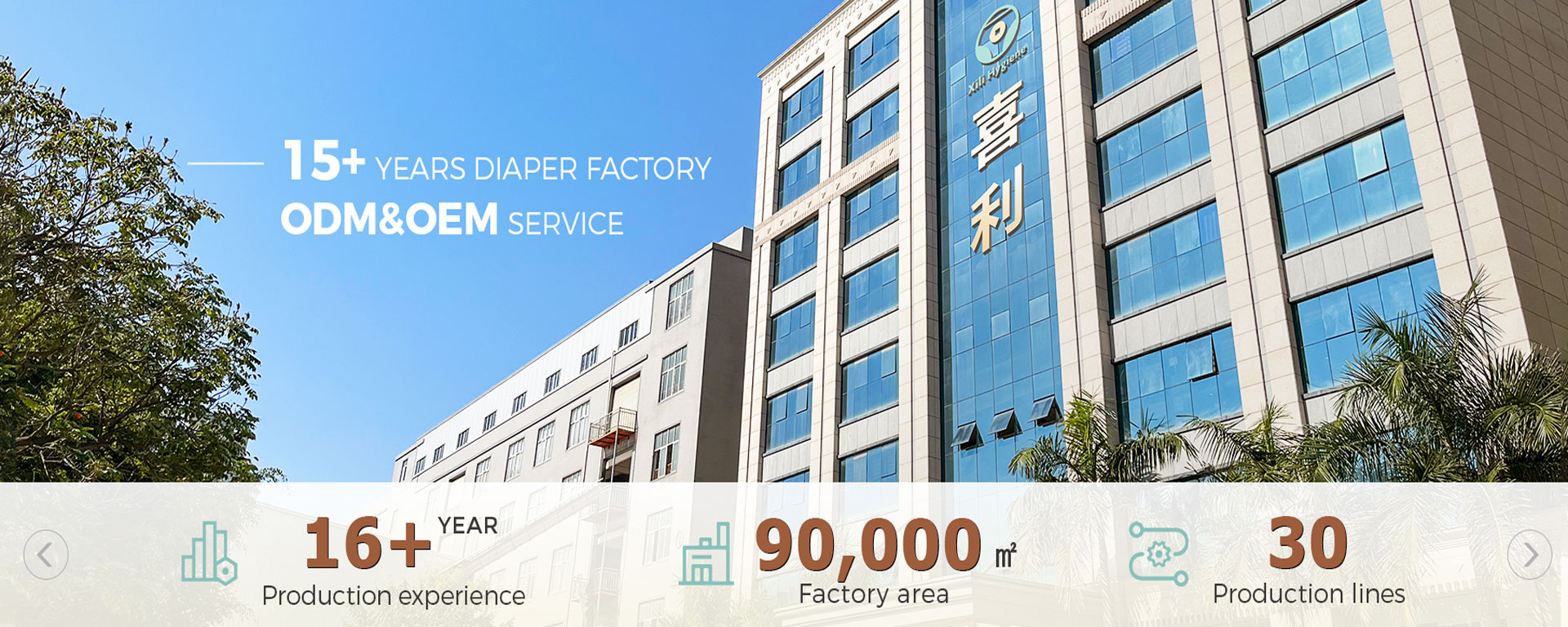
Comment la production de couches jetables
2022-10-20 11:52
Le processus de fabrication
Formation du coussin absorbant
1 Le coussin absorbant est formé sur une bande transporteuse mobile qui traverse une longue"chambre de formage."En divers points de la chambre, des buses sous pression pulvérisent soit des particules de polymère, soit un matériau fibreux sur la surface du convoyeur. Le fond du convoyeur est perforé, et lorsque le matériau du tampon est pulvérisé sur la bande, un vide est appliqué par le bas afin que les fibres soient tirées vers le bas pour former un tampon plat.
Au moins deux méthodes ont été employées pour incorporer des polymères absorbants dans le tampon. Dans un procédé, le polymère est injecté dans la même charge d'alimentation qui fournit les fibres. Cette méthode produit un tampon dont le polymère absorbant est dispersé uniformément sur toute sa longueur, sa largeur et son épaisseur. Les problèmes associés au procédé sont qu'une perte d'absorbant peut se produire parce que les fines particules sont tirées à travers les perforations du convoyeur par le vide. C'est donc cher et salissant. Cette méthode provoque également une absorption inégale du tampon puisque l'absorbant n'est perdu que d'un côté et pas de l'autre.
Un deuxième procédé d'application de polymère et de fibre implique l'application du matériau absorbant sur la surface supérieure du tampon après qu'il a été formé. Ce procédé produit un tampon qui a un matériau absorbant concentré sur sa face supérieure et n'a pas beaucoup d'absorbance dans tout le tampon. Un autre inconvénient est qu'un tampon fabriqué en
de cette façon peut perdre une partie du polymère appliqué à sa surface. De plus, cette approche a tendance à provoquer un blocage du gel, puisque tout l'absorbant se trouve à l'extérieur du tampon. L'humidité est emprisonnée dans cette couche externe et n'a aucune chance de se diffuser vers le centre. Ce blocage retient l'humidité contre la peau et peut entraîner une gêne pour le porteur.
Ces problèmes sont résolus en contrôlant le mélange polymère et matériau fibreux. Plusieurs distributeurs de pulvérisation sont utilisés pour appliquer plusieurs couches de polymère et de fibre. Au fur et à mesure que la fibre est étirée dans la chambre et que le fond du tampon est formé, une partie du polymère est ajoutée au mélange pour former une couche de polymère et de fibre combinés. Ensuite, plus de fibres pures sont tirées sur le dessus pour donner un effet sandwich. Cette formation crée un tampon avec le polymère absorbant confiné en son centre, entouré de matériau fibreux. Le blocage du gel n'est pas un problème car le polymère est concentré au cœur du tampon. Il résout également le problème de perte de particules puisque tout l'absorbant est entouré de matière fibreuse. Enfin, ce procédé est plus rentable car il distribue le polymère là où il est nécessaire.
2 Une fois que le tampon a reçu une dose complète de fibres et de polymère, il descend le chemin du convoyeur jusqu'à un rouleau de nivellement près de la sortie de la chambre de formage. Ce rouleau enlève une partie de la fibre au sommet du tampon pour lui donner une épaisseur uniforme. Le tampon se déplace ensuite par le convoyeur à travers la sortie pour des opérations ultérieures pour former la couche finie.
Préparation du non-tissé
3 Des feuilles de tissu non tissé sont formées à partir de résine plastique en utilisant le procédé de fusion-soufflage tel que décrit ci-dessus. Ces feuilles sont produites sous la forme d'un rouleau large connu sous le nom de"la toile,"qui est ensuite coupé à la largeur appropriée pour être utilisé dans les couches. Il y a une bande pour la feuille supérieure et une autre pour la feuille inférieure. Il convient de noter que cette étape ne se produit pas nécessairement en séquence après la formation du tampon car les tissus non tissés sont souvent fabriqués dans un emplacement séparé. Lorsque le fabricant est prêt à lancer la production de couches, ces gros boulons de tissu sont reliés à un équipement à rouleaux spécial qui alimente la chaîne de montage en tissu.
4 À un moment donné du processus, des bandes élastiques étirées sont fixées à la feuille de support avec de l'adhésif. Une fois la couche assemblée, ces bandes élastiques se contractent et rassemblent la couche pour assurer un ajustement parfait et limiter les fuites.
Assemblage des composants
5 À ce stade du processus, il y a encore trois composants distincts, le tampon absorbant, la feuille supérieure et la feuille de support. Ces trois composants sont en longues bandes et doivent être assemblés et coupés en unités de la taille d'une couche. Ceci est accompli en amenant le tampon absorbant sur un convoyeur avec la feuille de fond en polyéthylène. La feuille supérieure en polypropylène est ensuite mise en place et les feuilles compilées sont jointes par collage, chauffage ou soudage par ultrasons. La couche assemblée peut avoir d'autres attaches, telles que des bandes de ruban adhésif ou du Velcro™, qui agissent comme des fermetures.
6 Le long rouleau est ensuite coupé en couches individuelles, plié et emballé pour l'expédition.
Sous-produits/déchets
La production de couches ne produit pas de sous-produits importants; en fait, l'industrie des couches utilise les sous-produits d'autres industries. Les polymères absorbants utilisés dans la production de couches sont souvent des restes des lignes de production d'autres industries chimiques. Les particules de polymère sont trop petites pour d'autres applications, mais elles sont bien adaptées à une utilisation dans des couches. Dans la production de couches, cependant, des quantités considérables à la fois de matériau non tissé et de particules de polymère sont gaspillées. Pour minimiser ces déchets, l'industrie essaie d'optimiser le nombre de couches obtenues à partir de chaque mètre carré (mètre) de matériau. De plus, tous les efforts sont faits pour récupérer les fibres et le matériau polymère en excès utilisés dans la chambre de formage. Cependant, cela n'est pas toujours possible en raison du colmatage des filtres et d'autres pertes.
Contrôle de qualité
Il existe plusieurs méthodes utilisées pour contrôler la qualité des couches jetables, et la plupart d'entre elles concernent la capacité d'absorption du produit. L'une des clés consiste à s'assurer que le rapport polymère/fibre dans le tampon absorbant est correct. Trop de variation aura un impact sur la capacité de la couche à absorber l'humidité. Les essais et erreurs de l'industrie ont montré que pour des performances et un coût optimaux, le rapport fibres/particules devrait être d'environ 75:25 à 90:10. La taille et la distribution de ces particules sont encore plus critiques que ce rapport. Il a été établi que les particules ayant une granulométrie médiane en masse supérieure ou égale à environ 400 microns fonctionnent très bien avec les fibres pour améliorer la vitesse à laquelle le fluide est transporté hors du corps. Si les particules varient beaucoup en dehors de cette plage, un blocage du gel peut se produire.
Il existe plusieurs tests standard que l'industrie utilise pour établir l'absorption des couches. L'un est appelé mouillabilité à la demande ou absorbance gravimétrique. Ces tests évaluent ce que l'on appelle communément l'absorbance sous charge (AUL). L'AUL est définie comme la quantité de solution saline à 0,9 % absorbée par les polymères tout en étant soumis à une pression équivalente à 21 000 dynes, soit environ 0,30 lb/sq in (0,021 kg/sq cm). Ce test simule l'effet d'un bébé assis sur une couche mouillée. Si la couche a une capacité d'absorption d'au moins 24 ml/g après une heure, la qualité est considérée comme acceptable.
Outre l'absorption, d'autres facteurs de contrôle de la qualité sont liés à l'ajustement et au confort de la couche. Une attention particulière doit être accordée aux caractéristiques de fusion des tissus non tissés utilisés pour former l'enveloppe de la couche. Si des matériaux avec des points de fusion différents sont utilisés, le matériau qui fond le plus rapidement peut devenir trop mou et coller à l'appareil d'assemblage. Lorsque le tissu est retiré, il peut rester avec une surface rugueuse qui est inconfortable pour l'utilisateur. Enfin, l'alignement des composants doit être soigneusement vérifié ou des fuites peuvent en résulter.
Obtenez le dernier prix? Nous répondrons dès que possible (dans les 12 heures)